数控机床技术开展浅析。机床既是施行先进制造技术的重要配备,也是制造信息集成的一个重要载体,因而,机床的开展在一定水平上映射出加工技术的主要趋向。在20世纪后期构成的以数控技术为中心的柔性制造技术,预期在将来仍将持续停顿并成为加工技术开展的主流。它的特征能够归结为3F,3I和3S,即:
由高速切削推进至全面高速化,数控机床的主轴转速和功率的大幅度进步为高速切削提供了良好的条件。高速切削的界线,在不同的年代,随着切削办法和被加工资料的不同,其数值也不尽相同,通常以为的高速切削是指比传统的切削速度和进给速度高出5~8倍。图1 示出铣削不同金属资料时的高速切削范围。而高的进给速度在切削钢和铸铁时可达20~50m/min,相当每个刀齿的进给量为1.0-1.5mm。
显然高速加工能增大单位时间资料被切除的体积(资料切除率Q),但按目前机床的状况来看,要充沛发挥先进刀具的高速加工才能,还必需开发有更高驱动功率和构造刚度的机床,因而当前航空、汽车和模具等制造行业普遍地采用高速加工,并不是只限于进步切削效率,还着眼于用它在以下3方面取得对加工质量和经济效益的提升。
减小切削力,保证薄壁零件加工的外形精度。经过进步切削速度(Vc)和降低进给量(f),在坚持相同资料切除率Q的条件下,使每个刀齿的进给量减小而使切削力降低。
进步加工外表质量。在坚持相同的切削效率(即相同Q值)下,进步切削速度可改善切屑构成过程和增加切削阻尼有利于抑止颤振,而减少每个刀齿的进给量能降低切削外表轨迹构成的残留高度,改善外表粗糙度,从而有利于精细零件和模具的加工。
减少被加工零件的温升和热变形。高的切削速度和低的进给量所构成的连续切屑流将使更多的切削热被切屑带走,减少零件和刀具的热变形,有利于保证批量消费的零件尺寸稳定性。
因而,数控机床采取进步切削速度和切削进给后,对改善加工质量、缩短切削工时等有明显的效果,但为了到达机床应用率进一步进步的目的,还需对数控机床完成全面高速化。对现有数控机床运用状况统计得出:其有效切削时间与全部工时之比(机床应用率)仅为25%~35%,其他的75%~65%均耗费在机床调整、程序运转检查、空行程、起制动空运转、工件上下料和装夹等辅助时间以及待工时间(由于技术准备和调度不及时惹起的非工作时间)与毛病停机时间上。因而需经过进步各轴快移速度和加(减)速度、主轴变速的角加(减)速度、刀具(工件)自动交流速度,改善数控系统的操作便当性和监控功用以及增强信息管理才有可能全面紧缩辅助时间和减少待工时间,使数控机床的应用率到达60%以上。
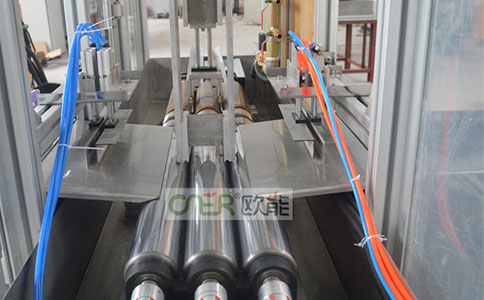